Fine Blanking
Fine Blanking Press
It is a method for plastic forming where the clearance between the punch and the die is minimized and the material is held with a guide plate and counter force.
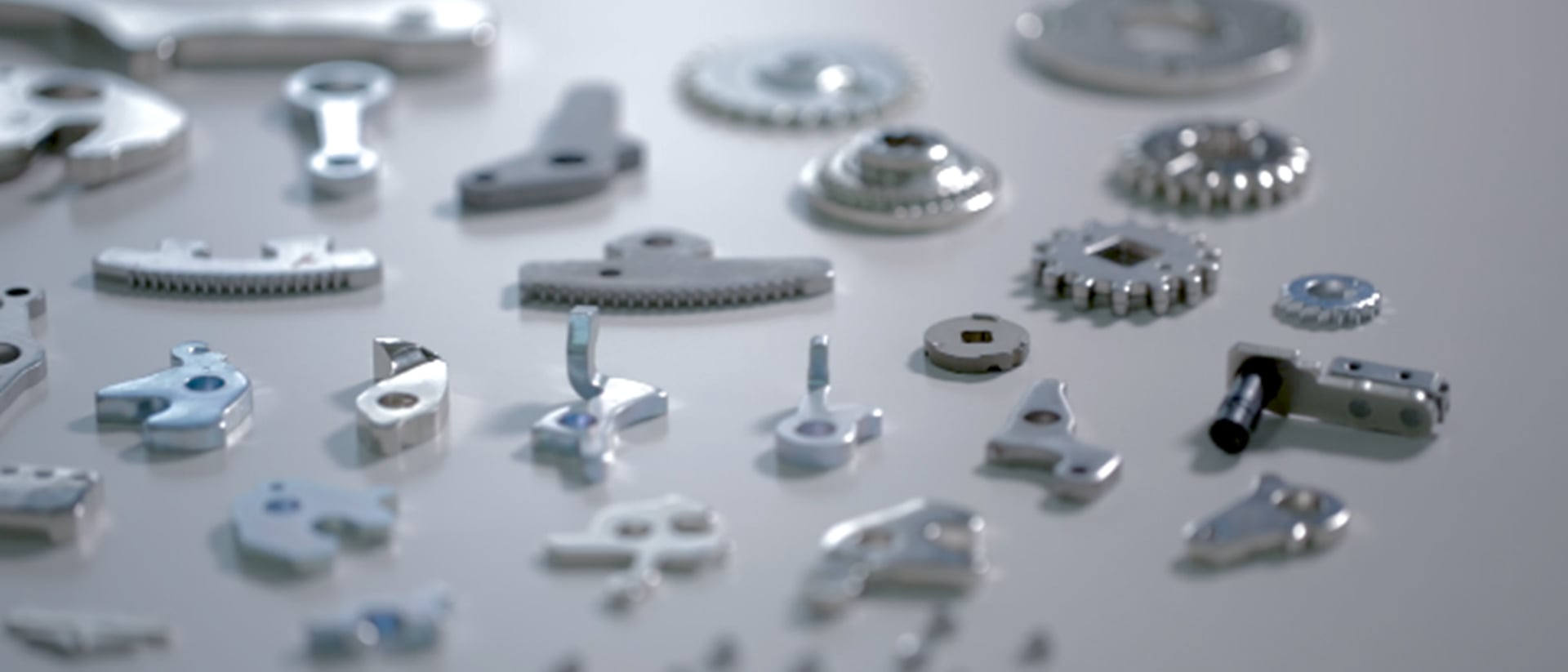
Overview
Compared to general punching press work, this method produces high-precision products with a smooth shear surface and exact squareness.
Fine blanking has attracted so much attention and spread because of the high potential of its basic principle.
Today, we are continuing to evolve this method, supported not only by various innovations and improvements, but also by additional peripheral technologies.
It is an excellent technology that contributes not only to the quality and performance of finished products, but also to the rationalization of processing, conservation of resources, and reduction of costs.
Features
Feature 01High precision with smooth shear surface and exact squareness.
Micron-level precision press is possible—something which is difficult with general press work. A smooth, beautiful shear surface can be obtained, with no need for post-treatment.
Feature 02Original technology for mold design
About 60 years have passed since the basic technology was acquired from a Swiss company Hydrel, and all of our molds are manufactured in-house. Based on our proprietary design philosophy, we continue to evolve in various processes, from mold design to the manufacture of press molded products.
The Company’s molds are designed and manufactured to have a 4-prop or 2-prop structure to provide rigidity with an emphasis on precision of products.
Feature 03Rationalization, resource conservation and cost reduction
It is an excellent technology that contributes not only to the quality and performance of finished products, but also to the rationalization of processing, conservation of resources, and reduction of costs.
Mechanism
-
General Punching Press
-
Fine Blanking Press
Process cycle
-
1
The press closes rapidly, and the rounded blades begin to compress into the material surface.
-
2
The rounded blades compress and start cutting.
-
3
The fine blanking operation is complete, with the product inside the die and the punching slag inside the punch.
-
4
The product and the punching slag are discharged, and the punch is separated from the material. Immediately after that, the product and slag are blown away with an air blower, etc., and the next material to process advances.
Processing examples
Products that undergo post-treatment after general pressing, forging, casting, etc. can be produced without post-treatment by using fine blanking.
-
General Punching Press
-
Smooth shear surface after fine blanking press
- Processing methods
-
-
-
-
Outer periphery chamfering
-
Internal chamfering
-
-
-
-
-
-
-
-
-
Improvement in hole surface roughness: Hole surface roughness can be improved to about 0.3 a, eliminating the need for the reamer honing process.
-
- Post-treatment
-
We also undertake post-treatment processes following fine blanking, such as deburring, polishing, heat treatment, surface treatment and machining.
-
Deburring
-
Heat treatment
-
Surface treatment
-
Resin molding
-
Line-up
Full processing line that leverages our know-how in press machine manufacturing
In this age where small quantities of products with high added value are abundant, responding to the demands of the market requires a variety of molds and related parts that meet each diverse need. The Company offers a broad line-up of fine blanking presses, ranging from 100 to 650t.
We offer products based on our abundant experience and technologies in fine blanking nurtured over many years along with our consistent management system.
Latch/Ratchet
The photo shown is just one example of parts related to door locks. Please let us know if you need any parts.
View List
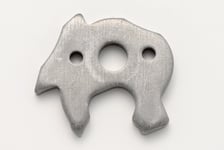
Plate thickness: 4.5mm
Material: SCM435
Application: Automotive parts
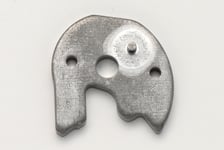
Plate thickness: 4.9mm
Material: SCM415
Application: Automotive parts
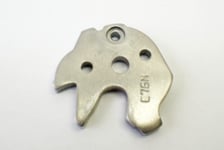
Plate thickness: 4.9mm
Material: SCM415
Application: Automotive parts
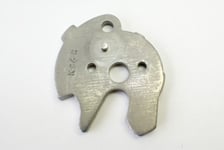
Plate thickness: 4.9mm
Material: SCM415
Application: Automotive parts
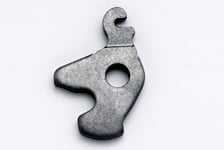
Plate thickness: 5mm
Material: SCM435
Application: Automotive parts
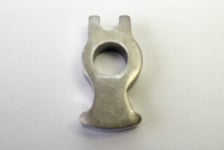
Plate thickness: 5mm
Material: SAPH44
Application: Automotive parts
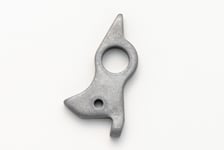
Plate thickness: 4mm
Material: SPHC
Application: Automotive parts
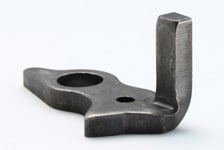
Plate thickness: 4mm
Material: SAPH44
Application: Automotive parts
Flange
The photo shown is just one example of piping-related parts. Please let us know if you need any parts.
View List
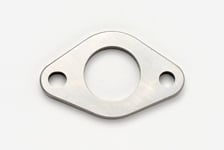
Plate thickness: 6mm
Material: SUS304
Application: Automotive parts
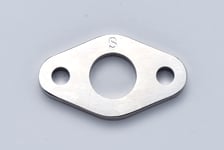
Plate thickness: 6mm
Material: SPHC
Application: Automotive parts
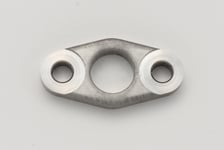
Plate thickness: 7mm
Material: SUS304K
Application: Automotive parts
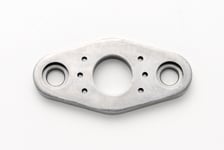
Plate thickness: 8mm
Material: SPHC
Application: Automotive parts
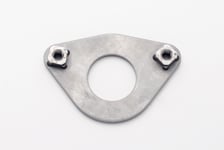
Plate thickness: 4.5mm
Material: SPHC
Application: Automotive parts
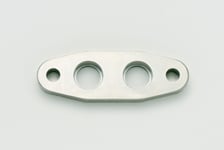
Plate thickness: 9mm
Material: SUS304
Application: Automotive parts
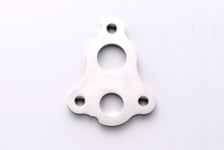
Plate thickness: 8mm
Material: SUS304
Application: Automotive parts
Gears
The photo shown is just one example of gear-related parts. Please let us know if you need any parts.
View List
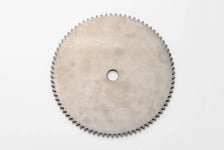
Plate thickness: 6mm
Material: SPHC
Application: Agricultural machinery
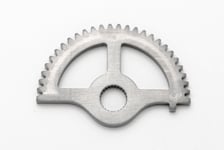
Plate thickness: 6mm
Material: SCM435
Application: Automotive parts
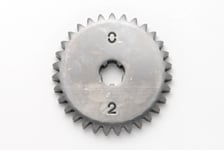
Plate thickness: 8.8mm
Material: S20C
Application: Crane parts
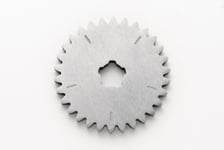
Plate thickness: 7.5mm
Material: SA1010
Application: Crane parts
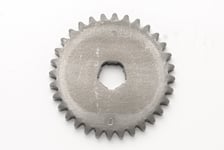
Plate thickness: 8mm
Material: SA1010
Application: Crane parts
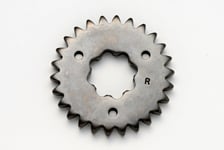
Plate thickness: 5.8mm
Material: SCM415
Application: Agricultural machinery
Other
The application and photograph shown are just examples of various fine blanking parts. Please let us know if you need any parts.
View List
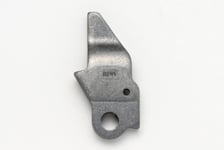
Plate thickness: 6mm
Material: SPHC
Application: Automotive parts
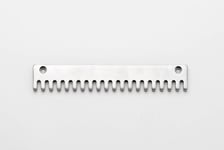
Plate thickness: 5mm
Material: SPHC
Application: Industrial machinery
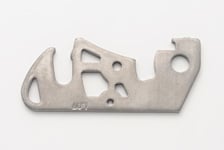
Plate thickness: 4mm
Material: SCM435
Application: Automotive parts
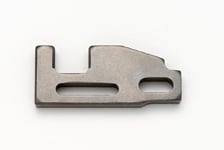
Plate thickness: 8.1mm
Material: SS400
Application: Automotive parts
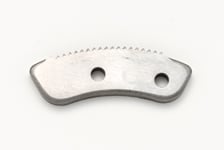
Plate thickness: 6mm
Material: Hot-rolled steel sheet
Application: Automotive parts
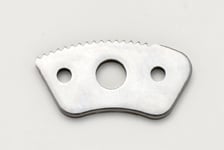
Plate thickness: 4.5mm
Material: Hot-rolled steel sheet
Application: Automotive parts
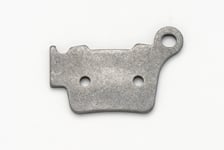
Plate thickness: 3.5mm
Material: S45C
Application: Two-wheel vehicle parts
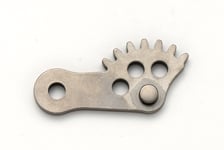
Material: Hot-rolled steel sheet
Application: Automotive parts
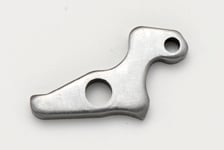
Plate thickness: 5mm
Material: SCM435
Application: Automotive parts
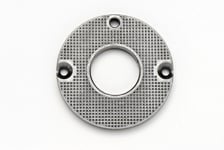
Plate thickness: 5.55mm
Material: KFN4
Application: Automotive parts
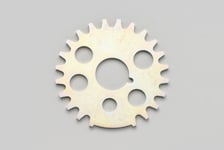
Plate thickness: 3.2mm
Material: SPFH59
Application: Two-wheel vehicle parts
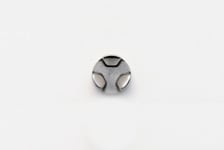
Material: Carbon tool steel
Application: Automotive parts
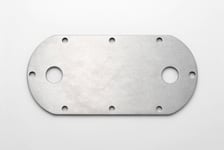
Plate thickness: 5mm
Material: SPHC
Application: Automotive parts
Installation Process
We offer custom-made products to meet customer needs, taking into consideration the application and environment of use.
- Mold fabrication period:4 months
-
-
1Mold design
-
2Drawing approval
-
3Mold manufacturing and assembly
-
4Trial testing and product inspection
-
5Customer approval
-
6Start of mass production
-